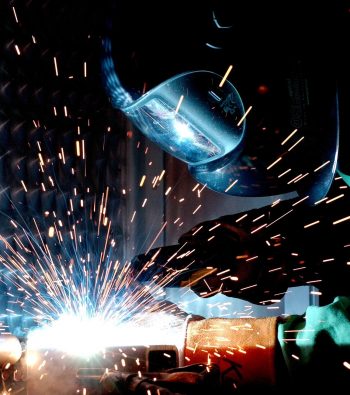
Authored by: Darrell Adams, Head of Southeast Asia & Oceania, Universal Robots
For small to mid-sized manufacturers, any gain in productivity can have a huge impact. Automation offers significant advantages, but many small and mid-sized enterprises (SMEs) believe that robotics is out of their reach. These organisations cannot afford large, complex robots that do not fit within their limited floor space. These complex robots require specialised personnel to program and maintain them, and that is simply too expensive, with a payback period that is too long to justify the investment.
A new generation of collaborative robots (or “cobots”) is changing the game for smaller manufacturers, helping them compete more effectively, offering new opportunities for employees, and even improving worker safety. Darrell Adams, Head of Southeast Asia & Oceania, Universal Robots, shares 5 essential requirements that will put robotics within SME’s reach.
- Quick set-up
Setting up a conventional industrial robot can take days or even weeks. These are the time and disruption that SMEs simply cannot afford. When ready to automate, manufacturers or any untrained operator need to be able to unpack the new robot, mount it, and begin programming simple tasks in a matter of hours. Collaborative robot arms, such as those from Universal Robots (UR), weigh as little as 11 kg, and can be set up in less than a day.
2. Improving the small business culture
Most SMEs operates with 50 to 250 employees, having a shared sense of culture among the small group of employees is important for SMEs. Businesses run best when employees enjoy their assigned jobs, encouraging productivity and efficiency. Having cobots to automate the monotonous and strenuous tasks give employees more freedom to take on better and more exciting roles. SMEs need not worry about releasing these employees as no robots can replace human creativity and critical thinking. Instead, SMEs are elevating employees’ job titles by retraining employees to work alongside robots.
PT JVC Electronics Indonesia (JEIN), a global leader in electronic and entertainment products, deployed seven units of Universal Robots’ UR3 cobots to increase productivity and achieve consistent quality. The adoption of UR3 lessened the burden on workers to perform menial and repetitive tasks. JEIN witnessed an improvement in production efficiency and stable quality of output. With the move towards automation, employees can be redeployed to other processes and operational costs were reduced by more than USD 80,000 yearly. With cobots working alongside humans, it helps to humanise labour, establishing a better company culture.
3. Collaborative and safe
Conventional industrial robots require a large, separate enclosure, which adds cost, takes up operational space, and reduces flexibility on the production floor. Management also has to be concerned with the safety risk if someone manages to get inside the enclosure while the robot is activated.
However, small manufacturers cannot afford to dedicate large areas to robotic operation. Today’s collaborative robots can work side-by-side with human workers in complementary operations. For example, the innovative force-sensing technology built into UR robots means the robot stops operating if it comes into contact with a human, and 80 per cent of the thousands of UR robots in operation worldwide work right beside human operators with no safety guarding (upon risk assessment).
4. Flexible deployment for multiple uses
Dedicated industrial robots can limit small and mid-sized manufacturers who often have small production batches and require fast change-overs. In contrast, new collaborative robots are lightweight, space-saving, and easy to redeploy to multiple locations without changing the production layout. With the ability to reuse programs for recurring tasks, they support agile manufacturing processes with minimal set-up time and effort.
5. Fast payback of your investment
Of course, any automation investment for a small or mid-sized manufacturer must pay for itself as quickly as possible. Universal Robots gives SMEs all the advantages of advanced robotic automation, with none of the traditional added costs associated with robot programming, set up, and dedicated, shielded work cells. With an average payback period as short as twelve months, robotic automation is finally affordable for small and mid-sized manufacturers.
Universal Robots believes that collaborative technology can be used to benefit all aspects of task-based businesses, regardless of their size. The nominal investment costs can be quickly recovered, such benefits from the latest collaborative technology should be available to all businesses.


Archive
- October 2024(44)
- September 2024(94)
- August 2024(100)
- July 2024(99)
- June 2024(126)
- May 2024(155)
- April 2024(123)
- March 2024(112)
- February 2024(109)
- January 2024(95)
- December 2023(56)
- November 2023(86)
- October 2023(97)
- September 2023(89)
- August 2023(101)
- July 2023(104)
- June 2023(113)
- May 2023(103)
- April 2023(93)
- March 2023(129)
- February 2023(77)
- January 2023(91)
- December 2022(90)
- November 2022(125)
- October 2022(117)
- September 2022(137)
- August 2022(119)
- July 2022(99)
- June 2022(128)
- May 2022(112)
- April 2022(108)
- March 2022(121)
- February 2022(93)
- January 2022(110)
- December 2021(92)
- November 2021(107)
- October 2021(101)
- September 2021(81)
- August 2021(74)
- July 2021(78)
- June 2021(92)
- May 2021(67)
- April 2021(79)
- March 2021(79)
- February 2021(58)
- January 2021(55)
- December 2020(56)
- November 2020(59)
- October 2020(78)
- September 2020(72)
- August 2020(64)
- July 2020(71)
- June 2020(74)
- May 2020(50)
- April 2020(71)
- March 2020(71)
- February 2020(58)
- January 2020(62)
- December 2019(57)
- November 2019(64)
- October 2019(25)
- September 2019(24)
- August 2019(14)
- July 2019(23)
- June 2019(54)
- May 2019(82)
- April 2019(76)
- March 2019(71)
- February 2019(67)
- January 2019(75)
- December 2018(44)
- November 2018(47)
- October 2018(74)
- September 2018(54)
- August 2018(61)
- July 2018(72)
- June 2018(62)
- May 2018(62)
- April 2018(73)
- March 2018(76)
- February 2018(8)
- January 2018(7)
- December 2017(6)
- November 2017(8)
- October 2017(3)
- September 2017(4)
- August 2017(4)
- July 2017(2)
- June 2017(5)
- May 2017(6)
- April 2017(11)
- March 2017(8)
- February 2017(16)
- January 2017(10)
- December 2016(12)
- November 2016(20)
- October 2016(7)
- September 2016(102)
- August 2016(168)
- July 2016(141)
- June 2016(149)
- May 2016(117)
- April 2016(59)
- March 2016(85)
- February 2016(153)
- December 2015(150)