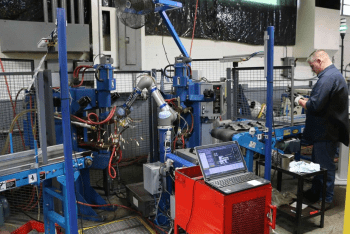
Universal Robots (UR), Denmark-based collaborative robots (cobots) technology market leader, urged local manufacturers to accelerate robotic automation and increase productivity, while reducing workplace injuries.
According to the Department of Occupational Safety and Health (DOSH) under Ministry of Human Resource, Malaysia recorded 5,422 occupational accidents from January to September 2020 alone with total deaths numbering 152. The accidents were most prevalent in manufacturing sector at 63.2%; agriculture, forestry and fisheries at 14.4%; and the remaining 22.4% across other industry sectors.
Most local manufacturers face a growing skilled talent shortage, which strains its overall productivity and growth. At the same time, employers are also facing immense costs associated with workplace-related injuries.
“Cobots can perform tasks that may be dangerous or injury-prone for humans. With built-in safety features that slow the robot arm when a human enters its workspace, cobots can keep human colleagues safe from occupational injuries as it addresses repetitive and dangerous tasks in the manufacturing sector,” said James McKew, Regional Director of Asia-Pacific in Universal Robots.
Universal Robots’ adjustable safety system allows companies to adjust a range of parameters to reduce the risks involved with implementing an industrial robot application. These include limiting the force, speed, power or momentum of the robot, or restricting its workspace using safety boundaries. Productivity gains and the inherently safe design of cobot solutions means this new automation technology could reduce up to 72% of the common causes of injury in manufacturing environments.
“As we move closer to the vision of Industry 5.0 – where man and machine work together on the smart factory floor, the need to consider the safety and compliance requirements of this new kind of workplace has become paramount. Undoubtedly, a collaborative workforce featuring human and robots complements each other in their roles and offers significant opportunities to enhance manufacturing productivity, innovation, safety and overall job satisfaction in the workplace,” added McKew.
McKew also pointed out that companies can achieve a faster Return on Investment (ROI) by using cobots to free up workers’ time, allowing them to tackle higher productivity processes and ultimately acquire new skills.
Unlike traditional robots that require engineer-level programming, cobots are designed to make programming simple through human-machine interfaces (HMI) familiar to anyone who has used a smartphone.
For more complex applications, Universal Robots has a comprehensive network of Certified System Integrators and Authorised Training Centres ready to support users with day-to-day operations after the initial installation. Such interfaces and capabilities make the skills gap and learning curve for using cobots diminishingly small by eliminating the need for formal education in programming or robotics. Universal Robots encourages local manufacturers to adopt the perfect man and machine collaboration.
With cobots, manufacturers in Malaysia need not fear the impacts caused by the growing skilled talent shortage. The collaboration greatly reduces time, effort and cost associated with using the same cobot for various tasks as a cobots’ flexibility translates to a significantly faster return on investment.


Archive
- October 2024(44)
- September 2024(94)
- August 2024(100)
- July 2024(99)
- June 2024(126)
- May 2024(155)
- April 2024(123)
- March 2024(112)
- February 2024(109)
- January 2024(95)
- December 2023(56)
- November 2023(86)
- October 2023(97)
- September 2023(89)
- August 2023(101)
- July 2023(104)
- June 2023(113)
- May 2023(103)
- April 2023(93)
- March 2023(129)
- February 2023(77)
- January 2023(91)
- December 2022(90)
- November 2022(125)
- October 2022(117)
- September 2022(137)
- August 2022(119)
- July 2022(99)
- June 2022(128)
- May 2022(112)
- April 2022(108)
- March 2022(121)
- February 2022(93)
- January 2022(110)
- December 2021(92)
- November 2021(107)
- October 2021(101)
- September 2021(81)
- August 2021(74)
- July 2021(78)
- June 2021(92)
- May 2021(67)
- April 2021(79)
- March 2021(79)
- February 2021(58)
- January 2021(55)
- December 2020(56)
- November 2020(59)
- October 2020(78)
- September 2020(72)
- August 2020(64)
- July 2020(71)
- June 2020(74)
- May 2020(50)
- April 2020(71)
- March 2020(71)
- February 2020(58)
- January 2020(62)
- December 2019(57)
- November 2019(64)
- October 2019(25)
- September 2019(24)
- August 2019(14)
- July 2019(23)
- June 2019(54)
- May 2019(82)
- April 2019(76)
- March 2019(71)
- February 2019(67)
- January 2019(75)
- December 2018(44)
- November 2018(47)
- October 2018(74)
- September 2018(54)
- August 2018(61)
- July 2018(72)
- June 2018(62)
- May 2018(62)
- April 2018(73)
- March 2018(76)
- February 2018(8)
- January 2018(7)
- December 2017(6)
- November 2017(8)
- October 2017(3)
- September 2017(4)
- August 2017(4)
- July 2017(2)
- June 2017(5)
- May 2017(6)
- April 2017(11)
- March 2017(8)
- February 2017(16)
- January 2017(10)
- December 2016(12)
- November 2016(20)
- October 2016(7)
- September 2016(102)
- August 2016(168)
- July 2016(141)
- June 2016(149)
- May 2016(117)
- April 2016(59)
- March 2016(85)
- February 2016(153)
- December 2015(150)