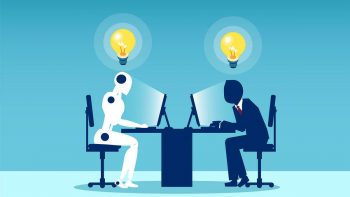
Authored by: James McKew, Regional Director Asia-Pacific Universal Robots
More than a year on with COVID-19 has taught us to expect the unexpected. Manufacturers have always been highly attuned to change, but the pandemic hit the manufacturing industry seemingly overnight, causing deep and long-lasting impacts. We can look back and see what manufacturers have learned about how to adapt and succeed in the face of adversity.
The strategy for manufacturers to succeed in a VUCA world
The term VUCA refers to “volatile, uncertain, complex, and ambiguous” conditions. For manufacturers, automation has emerged as the single most powerful tactic for succeeding in a VUCA world, whether that is caused by a pandemic or almost any other business challenge. For decades, automation has helped manufacturers improve continuity, flexibility, competitiveness, productivity, and employee safety. In today’s VUCA world, manufacturers are increasingly turning to collaborative automation. A flexible, easy-to-use collaborative robot (cobot) is a natural fit when changes occur quickly, reducing the time to plan, budget, hire, and train employees for new skills, or undertake extensive plant and company reconfigurations.
Irrigation equipment is critical for Indian agriculture and demand is high, but many firms have been hit hard by staff absences due to the pandemic. One of India’s leading agricultural equipment manufacturers, Krishi Group, was faced a 40 to 50 per cent reduction in its workforce and struggled to keep up with demand until a Universal Robots (UR) cobot was introduced to its facility. The cobot now works alongside a human on quality control tasks that previously required two workers to complete.
Supply chains need a “plan B”
The pandemic hit the global supply chain quickly and acutely, exposing the vulnerability that had been building up for years. Manufacturers now know that they need a “Plan B” in case remote production or supply is compromised and market demands shift. Many manufacturers have realised the advantage of being closer to their customers, even if that keeps them in regions with higher labour costs.
The key is to be able to manage workers in terms of their availability and safety and to increase their value and skills to meet new production needs. Cobots can help businesses of all sizes anticipate and respond more effectively to change, turning unexpected obstacles into new opportunities.
Labour shortages lead to opportunity
Previous offshoring trends were fuelled by the dependence on lower-cost labour. Advances in cobots have drastically increased productivity and reduced costs across a number of manufacturing processes. Many of these can now be easily restored and deployed domestically. While labour rates in traditionally low-cost countries have seen annual increases in the double digits as well as the shortage of skilled labour, affordable cobots make automation even more accessible, independent of the company size.
PLC Industries, a Singapore-based service provider in precision engineering, was facing problems finding skilled labour and issues related to rising material and real estate costs. Therefore, the company decided to deploy two UR10 cobots at the production site in Singapore to overcome the challenges. The flexibility of UR10 allows a single worker to attend to four CNC machines. With the capability to work alongside human workers and the ease of use, this solves problems regarding the shortage of skilled labour. PLC Industries have witnessed an increase in production variety, boosting output by 40 per cent.
Meeting new safety requirements
The importance of physical distancing during COVID-19 has made infection control a new priority, and for many manufacturers, this new reality will continue indefinitely. Many successful manufacturers were able to reopen their doors more quickly with collaborative robots. By inserting UR cobots within standard production lines, these companies were able to offset face-to-face risks and create a safe distance between workers while keeping output levels high.
Multinational computer technology manufacturer Dell was looking to increase its production efficiency by automating its electronics assembly lines and testing facilities at their plant in Chennai – one of Dell’s only ten manufacturing plants in the world. The company deployed a UR cobot in 2017 for end of line packaging. After witnessing a reduction in ergonomic risks that Dell’s workers once faced and with the current COVID-19 challenges, the company has deployed 3 more cobots, increasing production efficiency while maintaining safety. Dell has found their cobots to be of additional value in the COVID-19 pandemic when the company has production demands to meet but must comply with physical distancing measures and ensure the safety of employees.
In many ways, manufacturers are navigating uncharted territories, but now more than a year on through the pandemic, we are finally seeing a promising future. Thanks to cobots, manufacturers are discovering innovative new opportunities to address a VUCA world and emerge smarter, sharper, and better prepared for any situation.


Archive
- October 2024(44)
- September 2024(94)
- August 2024(100)
- July 2024(99)
- June 2024(126)
- May 2024(155)
- April 2024(123)
- March 2024(112)
- February 2024(109)
- January 2024(95)
- December 2023(56)
- November 2023(86)
- October 2023(97)
- September 2023(89)
- August 2023(101)
- July 2023(104)
- June 2023(113)
- May 2023(103)
- April 2023(93)
- March 2023(129)
- February 2023(77)
- January 2023(91)
- December 2022(90)
- November 2022(125)
- October 2022(117)
- September 2022(137)
- August 2022(119)
- July 2022(99)
- June 2022(128)
- May 2022(112)
- April 2022(108)
- March 2022(121)
- February 2022(93)
- January 2022(110)
- December 2021(92)
- November 2021(107)
- October 2021(101)
- September 2021(81)
- August 2021(74)
- July 2021(78)
- June 2021(92)
- May 2021(67)
- April 2021(79)
- March 2021(79)
- February 2021(58)
- January 2021(55)
- December 2020(56)
- November 2020(59)
- October 2020(78)
- September 2020(72)
- August 2020(64)
- July 2020(71)
- June 2020(74)
- May 2020(50)
- April 2020(71)
- March 2020(71)
- February 2020(58)
- January 2020(62)
- December 2019(57)
- November 2019(64)
- October 2019(25)
- September 2019(24)
- August 2019(14)
- July 2019(23)
- June 2019(54)
- May 2019(82)
- April 2019(76)
- March 2019(71)
- February 2019(67)
- January 2019(75)
- December 2018(44)
- November 2018(47)
- October 2018(74)
- September 2018(54)
- August 2018(61)
- July 2018(72)
- June 2018(62)
- May 2018(62)
- April 2018(73)
- March 2018(76)
- February 2018(8)
- January 2018(7)
- December 2017(6)
- November 2017(8)
- October 2017(3)
- September 2017(4)
- August 2017(4)
- July 2017(2)
- June 2017(5)
- May 2017(6)
- April 2017(11)
- March 2017(8)
- February 2017(16)
- January 2017(10)
- December 2016(12)
- November 2016(20)
- October 2016(7)
- September 2016(102)
- August 2016(168)
- July 2016(141)
- June 2016(149)
- May 2016(117)
- April 2016(59)
- March 2016(85)
- February 2016(153)
- December 2015(150)