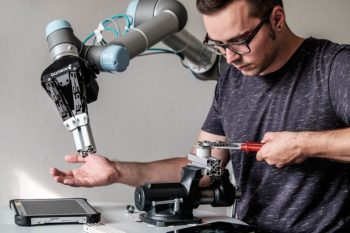
Authored By: James McKew, Regional President APAC – Universal Robots
Automation and robotics are often credited for their increased productivity and efficiency. Various sectors, especially manufacturing, construction and automotive, have relied heavily on industrial robots to achieve greater production output. Over the last 30 years, the capabilities of these large and bulky machines improved and transformed countless industrial processes. Built for sheer power and speed, traditional industrial robots, though powerful, presented safety risks to human workers.
In recent years, global economic uncertainties and unprecedented crises have upended many aspects of life, from the way people live, to people’s outlook of work, to the incorporation of new business models. This also means that the factors that made a manufacturer successful historically have changed: for example, the health and safety of employees have taken precedence over productivity and efficiency.
Reducing Workplace Injuries with Cobots
According to the Workplace Safety and Health Report 2021 by the Ministry of Manpower, there was a total of 12,766 workplace injuries reported in Singapore last year. Compared to the 11,350 workplace injuries reported in 2020, there was an 11% increase in the number of occupational injuries in 2021.
“In recent years, global economic uncertainties and unprecedented crises have upended many aspects of life, from the way people live, to people’s outlook of work, to the incorporation of new business models.”
In 2021, the top contributing sector/industry for major injuries in Singapore was manufacturing sector with 141 major injuries, these figures are high and the effects of accidents in workplaces can be shocking to manufacturers. Hence, manufacturers have radically shifted to accommodate new employees’ needs and aim to provide employees with a safe working environment. The beliefs and factors that supported years of consistent growth may no longer be valid.
This is where collaborative robots, or cobots, come in. Collaborative automation is changing the landscape and empowering employees. Cobots are far from the dangerous equipment planted at factory floors. Unlike traditional industrial robots that require safety cages to keep employees out of the workspace, cobots are designed to work alongside human workers without safety cages (upon risk assessment). While people misunderstand that robots are dangerous, cobots have managed to unravel these misconceptions. Recognised as the perfect man-machine collaboration, cobots are safe enough to function around human workers.
For Koyo Electronics Industries, a manufacturer of electronic equipment based in Japan, safety is placed a high priority on the manufacturing floor. The UR cobots feature safety functions such as protective stops. With built-in safety features, the cobots can operate safely without the installation of safety fences. This was a decisive factor in the implementation of UR cobots at Koyo Electronics Industries.
Cobots Boost Capacity and Job Satisfaction
While preventing workplace accidents is imperative, nurturing employees’ well-being is crucial in creating workplace resilience. Performing monotonous repetitive tasks such as heavy lifting, loading and unloading can lead to repetitive strain injuries. In this case, the deployment of cobots relieves human workers from the strenuous tasks, freeing them to work on higher value tasks that require humans’ cognitive abilities.
This was the case for BTC Mold, a Taiwan-based “full-process” manufacturer of plastic injection moulds. Initially, large machines were deployed at its production line. However, the manufacturer was faced with ongoing problems such as noise pollution and safety and space constraints caused by the traditional automated equipment. Despite adopting automation solutions, ensuring the well-being of employees remains optimal becomes a challenge for BTC Mold.
Before cobots were introduced, the packing of products was done manually; human workers were required to bend over when placing the products into boxes, causing joint pains and muscle aches after a prolonged period of time. The introduction of UR cobots relieved the workers from repetitive tasks, further reducing their risk of occupational accidents caused by extensive periods of hard labour. Now, 11% of BTC’s Mold’s manufacturing processes are supported by UR cobots. The manufacturer has solved work environmental issues and created safe working conditions for employees with the introduction of cobots.
“While preventing workplace accidents is imperative, nurturing employees’ well-being is crucial in creating workplace resilience.”
Manufacturing-related jobs often involve dull, dirty or dangerous tasks, potentially leading to workplace injuries and serious health complications. While workplace injuries may be deemed common in the manufacturing sector, such accidents can be significantly reduced. Collaborative automation has become increasingly capable of mitigating safety risks and improving employees’ well-being. Gone are the days when monotonous and repetitive tasks are conducted manually by humans. Cobots, the accessible automation option, is here to stay, offering a safe solution for manufacturers.


Archive
- October 2024(44)
- September 2024(94)
- August 2024(100)
- July 2024(99)
- June 2024(126)
- May 2024(155)
- April 2024(123)
- March 2024(112)
- February 2024(109)
- January 2024(95)
- December 2023(56)
- November 2023(86)
- October 2023(97)
- September 2023(89)
- August 2023(101)
- July 2023(104)
- June 2023(113)
- May 2023(103)
- April 2023(93)
- March 2023(129)
- February 2023(77)
- January 2023(91)
- December 2022(90)
- November 2022(125)
- October 2022(117)
- September 2022(137)
- August 2022(119)
- July 2022(99)
- June 2022(128)
- May 2022(112)
- April 2022(108)
- March 2022(121)
- February 2022(93)
- January 2022(110)
- December 2021(92)
- November 2021(107)
- October 2021(101)
- September 2021(81)
- August 2021(74)
- July 2021(78)
- June 2021(92)
- May 2021(67)
- April 2021(79)
- March 2021(79)
- February 2021(58)
- January 2021(55)
- December 2020(56)
- November 2020(59)
- October 2020(78)
- September 2020(72)
- August 2020(64)
- July 2020(71)
- June 2020(74)
- May 2020(50)
- April 2020(71)
- March 2020(71)
- February 2020(58)
- January 2020(62)
- December 2019(57)
- November 2019(64)
- October 2019(25)
- September 2019(24)
- August 2019(14)
- July 2019(23)
- June 2019(54)
- May 2019(82)
- April 2019(76)
- March 2019(71)
- February 2019(67)
- January 2019(75)
- December 2018(44)
- November 2018(47)
- October 2018(74)
- September 2018(54)
- August 2018(61)
- July 2018(72)
- June 2018(62)
- May 2018(62)
- April 2018(73)
- March 2018(76)
- February 2018(8)
- January 2018(7)
- December 2017(6)
- November 2017(8)
- October 2017(3)
- September 2017(4)
- August 2017(4)
- July 2017(2)
- June 2017(5)
- May 2017(6)
- April 2017(11)
- March 2017(8)
- February 2017(16)
- January 2017(10)
- December 2016(12)
- November 2016(20)
- October 2016(7)
- September 2016(102)
- August 2016(168)
- July 2016(141)
- June 2016(149)
- May 2016(117)
- April 2016(59)
- March 2016(85)
- February 2016(153)
- December 2015(150)