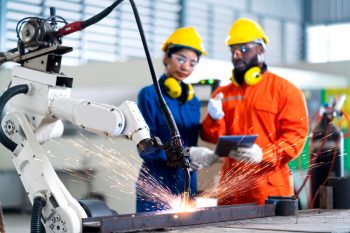
Attributed by Sandeep Bhargava, SVP, Global Services and Solutions, Public Cloud Business Unit, Rackspace Technology
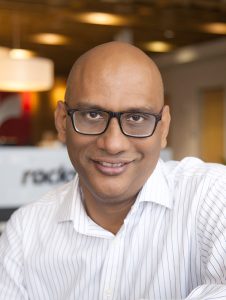
Sandeep Bhargava, SVP, Global Services and Solutions, Public Cloud Business Unit, Rackspace Technology
The booming manufacturing industry in Asia-Pacific is about to change. Modern infrastructure and applications were originally adopted slowly, but today they are embraced quickly, thanks to the rise of digital twins, robotics, cloud and edge computing, artificial intelligence (AI), and especially generative AI. By 2027, IDC predicts that 60% of Asia-Pacific organisations, will use automation to supplement operational jobs and increase employee engagement.
In recent news, the Malaysian Industrial Development Finance Bhd (MIDF) has approved soft loans totalling RM103.54 million to automate and modernise 29 companies as an incentive to embrace smart manufacturing using Industry 4.0 (IR4.0). Modernisation is not without difficulties, though. Manufacturers in Malaysia must take into account the potential and challenges that will shape the industry as it enters the world of artificial intelligence and cloud computing.
Capitalising on emerging technology
Forecasts indicate that the manufacturing sector will generate value added of US$118.5 billion (RM560.51 billion). With the increasing influx of high-tech and innovation-driven investments in Malaysia, especially in the green manufacturing and renewable sectors, the New Industrial Master Plan (NIMP) 2030 plan seeks to support Environmental, Social, and Governance (ESG) goals while increasing workforce productivity.
Manufacturers must adopt an integrated strategy using the cloud if they hope to successfully utilise these advancements and propel end-to-end transformation. To achieve this, they must expand on the skill sets they have already acquired during their transformation journeys, particularly in big data and analytics.
More precisely, since data is essential to intelligent production, manufacturers must figure out how to do it. Businesses now have access to enormous volumes of data that have the potential to completely change their operations because of the usage of increased Internet of Things (IoT) devices. Nevertheless, converting large amounts of data from many systems into useful insights is a difficult task.
To meet this problem, organisations can take advantage of AI’s wide range of capabilities to enable thorough data integration. With this degree of connection, customised centralised dashboards may offer real-time notifications at every stage of the operation. The enterprise-wide visibility offered, when combined with digital twins, will enable manufacturers to make more intelligent and efficient operational and business decisions.
By effectively utilising these resources, manufacturers will be able to analyse data from many departments inside the company, personalise both internal and external tools, and improve visibility to facilitate improved decision-making. The foundations of effective data and knowledge sharing are AI and the cloud. Organisations are able to lay out a plan that facilitates flexibility and adaptability when they have a strong feedback loop.
One firm that has effectively leveraged artificial intelligence is Cerapedics, a pioneer in biological bone grafting. The business created an IoT-enabled smart factory to scale. Through the use of a cloud environment, they were able to integrate both digital and analogue sensors, providing real-time insights that allowed for predictive maintenance and future growth prospects. Strict data collecting was a part of the process to guarantee regulatory compliance.
Manufacturing will be driven into the future by embracing these changes as a strategic shift, which will also enable new operational paradigms and help realise the full potential of the industrial IoT.
Prospective challenges
Even though modernisation—especially AI-driven modernisation—is pervasive in businesses, serious security issues persist. According to Rackspace’s Technology FAIR 2024 AI Research report, hardly 50% of participants indicated that their companies adhere to data management and retention regulations. Furthermore, 55% of respondents are cautious about the risks AI poses to cybersecurity.
Over half of the respondents indicated that their AI governance initiatives are centred on the responsible and ethical use of AI, indicating that ethics is another important concern. When asked to define “Responsible AI,” 52% of respondents said accountability, and 60% thought it had to do with data privacy. Fifty percent of the respondents mentioned transparency. This emphasises how crucial it is to first establish the governance framework to guarantee that AI risks are appropriately reduced and controlled.
Importantly, relative to AI adoption rates, there are fewer people concerned about AI governance, suggesting that IT leaders may be placing too much faith and security in AI systems. This is something that needs to be taken care of right now.
In terms of talent, Rackspace Technology discovered that businesses are working hard to close the skills gaps in software development and data analytics (40%), machine learning, and data engineering (43%), and data governance (38%). The majority of organisations don’t provide formalised training programs, which is the issue. Just about 40% of businesses offer AI training, but about 58% indicate they intend to do so in the future.
Thankfully, there are remedies available for the problems mentioned above. It is the responsibility of manufacturers to make wise decisions and plans. Manufacturers need to move to the cloud and work with professionals who can tailor tools and solutions to meet their specific demands as an organisation and business. Manufacturers may lay a strong basis for industrial innovation by working with the right partners.


Archive
- October 2024(44)
- September 2024(94)
- August 2024(100)
- July 2024(99)
- June 2024(126)
- May 2024(155)
- April 2024(123)
- March 2024(112)
- February 2024(109)
- January 2024(95)
- December 2023(56)
- November 2023(86)
- October 2023(97)
- September 2023(89)
- August 2023(101)
- July 2023(104)
- June 2023(113)
- May 2023(103)
- April 2023(93)
- March 2023(129)
- February 2023(77)
- January 2023(91)
- December 2022(90)
- November 2022(125)
- October 2022(117)
- September 2022(137)
- August 2022(119)
- July 2022(99)
- June 2022(128)
- May 2022(112)
- April 2022(108)
- March 2022(121)
- February 2022(93)
- January 2022(110)
- December 2021(92)
- November 2021(107)
- October 2021(101)
- September 2021(81)
- August 2021(74)
- July 2021(78)
- June 2021(92)
- May 2021(67)
- April 2021(79)
- March 2021(79)
- February 2021(58)
- January 2021(55)
- December 2020(56)
- November 2020(59)
- October 2020(78)
- September 2020(72)
- August 2020(64)
- July 2020(71)
- June 2020(74)
- May 2020(50)
- April 2020(71)
- March 2020(71)
- February 2020(58)
- January 2020(62)
- December 2019(57)
- November 2019(64)
- October 2019(25)
- September 2019(24)
- August 2019(14)
- July 2019(23)
- June 2019(54)
- May 2019(82)
- April 2019(76)
- March 2019(71)
- February 2019(67)
- January 2019(75)
- December 2018(44)
- November 2018(47)
- October 2018(74)
- September 2018(54)
- August 2018(61)
- July 2018(72)
- June 2018(62)
- May 2018(62)
- April 2018(73)
- March 2018(76)
- February 2018(8)
- January 2018(7)
- December 2017(6)
- November 2017(8)
- October 2017(3)
- September 2017(4)
- August 2017(4)
- July 2017(2)
- June 2017(5)
- May 2017(6)
- April 2017(11)
- March 2017(8)
- February 2017(16)
- January 2017(10)
- December 2016(12)
- November 2016(20)
- October 2016(7)
- September 2016(102)
- August 2016(168)
- July 2016(141)
- June 2016(149)
- May 2016(117)
- April 2016(59)
- March 2016(85)
- February 2016(153)
- December 2015(150)